Clemson Formula SAE Project Continues with SHD Inc. Support
Project update from Clemson Formula:
Take a look at Part 1 - Clemson Formula
To take advantage of our SHD sponsored materials, we used a variety of techniques and processes for layups. Our composite components could be divided into three categories: flat carbon-only elements, flat sandwich panels, and 3d components. Flat elements included spars, ribs, endplates, nose top, floor, steering wheel, control arm covers, and swan necks.
For these components, a quarter-inch steel plate was used as a molding surface to ensure that the surface would not warp when exposed to heat. To prep the plate, it was first sanded at increasing levels of grit to remove any previous materials and imperfections from the surface. Next, three layers of wax were applied and removed to fill in surface imperfections of the sheet without adding additional material to already flat areas. Next, three layers of polyvinyl alcohol release film were painted onto the surface to ease the release of parts from the mold. These mold prep steps were repeated for all molds that were used with composites.
For 3D components such as the swan necks, firewall, body panels, and headrest, individual mold materials were selected based on the desired size and properties of the final part. For body panels, we wanted to complete each side in a single layup, meaning that a dense tooling foam was the best material due to its large size and ease of tooling. Molds were CNC milled out of blanks, then surface imperfections and gaps were sealed with layers of bondo and duratec. Once these imperfections were filled, the mold was sanded down to a smooth finish and prepped. For the headrest and firewall, aluminum sheets were used to save cost and were bent and welded into the appropriate shapes. For the swan necks, the flat mold was used with the addition of two steel wedges to add angled tabs at the airfoil mounting points. Introducing this slight angle helped us to increase the lateral stiffness of the rear wing without adding additional supports.
Taking into account expected loads for each part, a layup schedule was selected to meet our factor of safety as well as weight goals. For load bearing components such as the cockpit floor, swan necks, air foil ribs, and endplates, sandwich panel layups were done with nomex honeycomb, SHD film adhesive, and SHD 12k prepreg to increase the overall strength and durability of our components. We emphasized strength on all the components that had an effect on driver safety such as all cockpit support and the steering wheel. Despite added carbon to increase strength, we still produced the lightest 4-cylinder car at competition in Michigan. This strength was put to the test during autocross running at Michigan when a cone hit the outside of the front wing which induced a torsional load through the main airfoil ribs. Despite the severity of the hit, all of the composite components completely survived the impact. Additionally, design judges were impressed with the rigidity of our rear wing thanks to the SHD 12k prepreg that was used to produce swan necks, endplates, ribs, and spars. For non-structural components including body panels, control arm covers, and the nose top, SHD 3k prepreg was used to maximize the strength of our components at the minimum possible weight. These parts produced a smooth surface finish which was beneficial to minimizing the skin friction drag of our car. In addition to increased strength and reduced weight, the use of prepreg significantly increased the efficiency of our composite manufacturing. Prepreg layups minimized the number of manufacturing steps per part, meaning we could produce parts more quickly and even complete multiple layups simultaneously for some components.
Thanks to our SHD sponsored materials, we were able to surpass our design goals for the 2023 season and produce a light, durable, and sleek car.
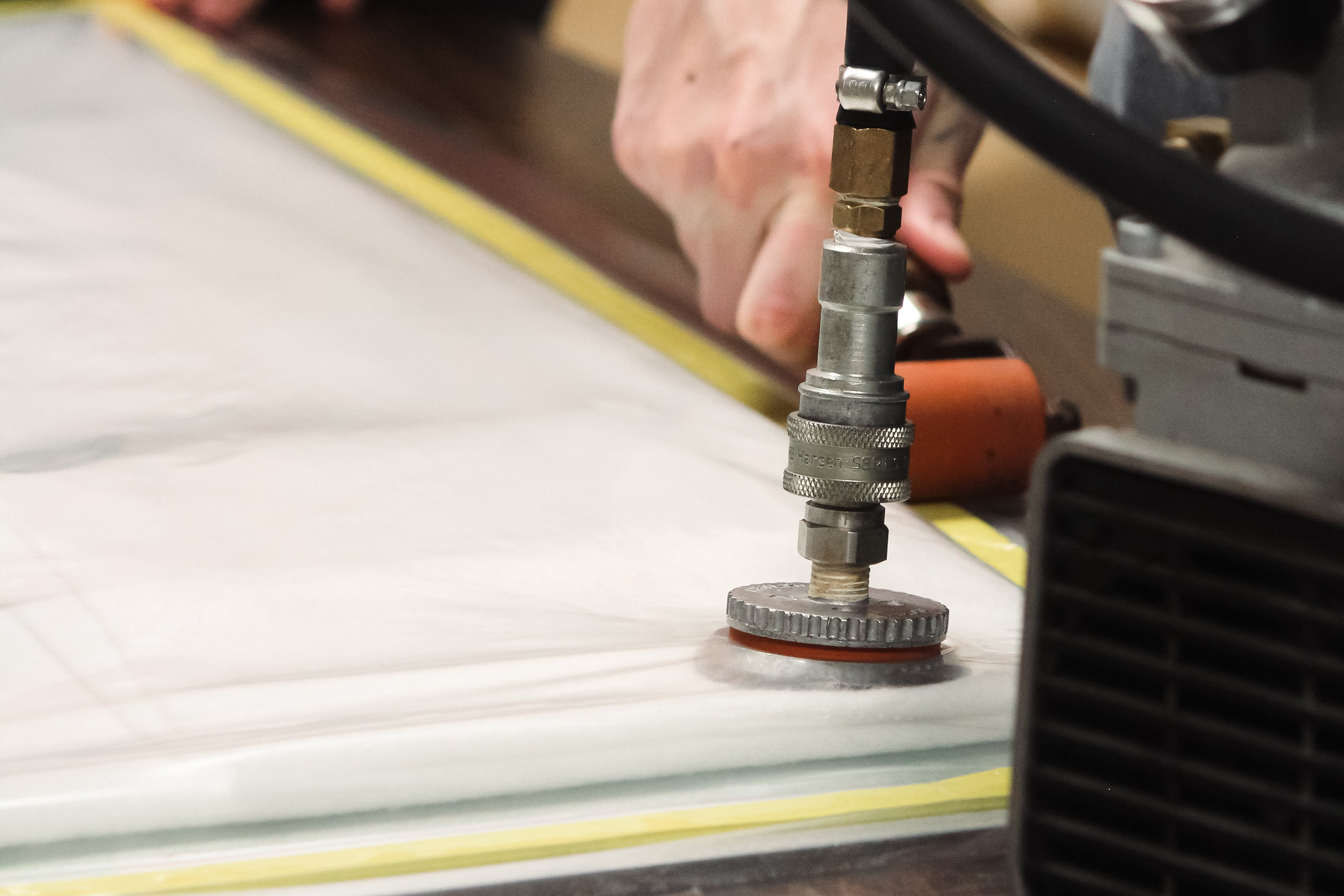
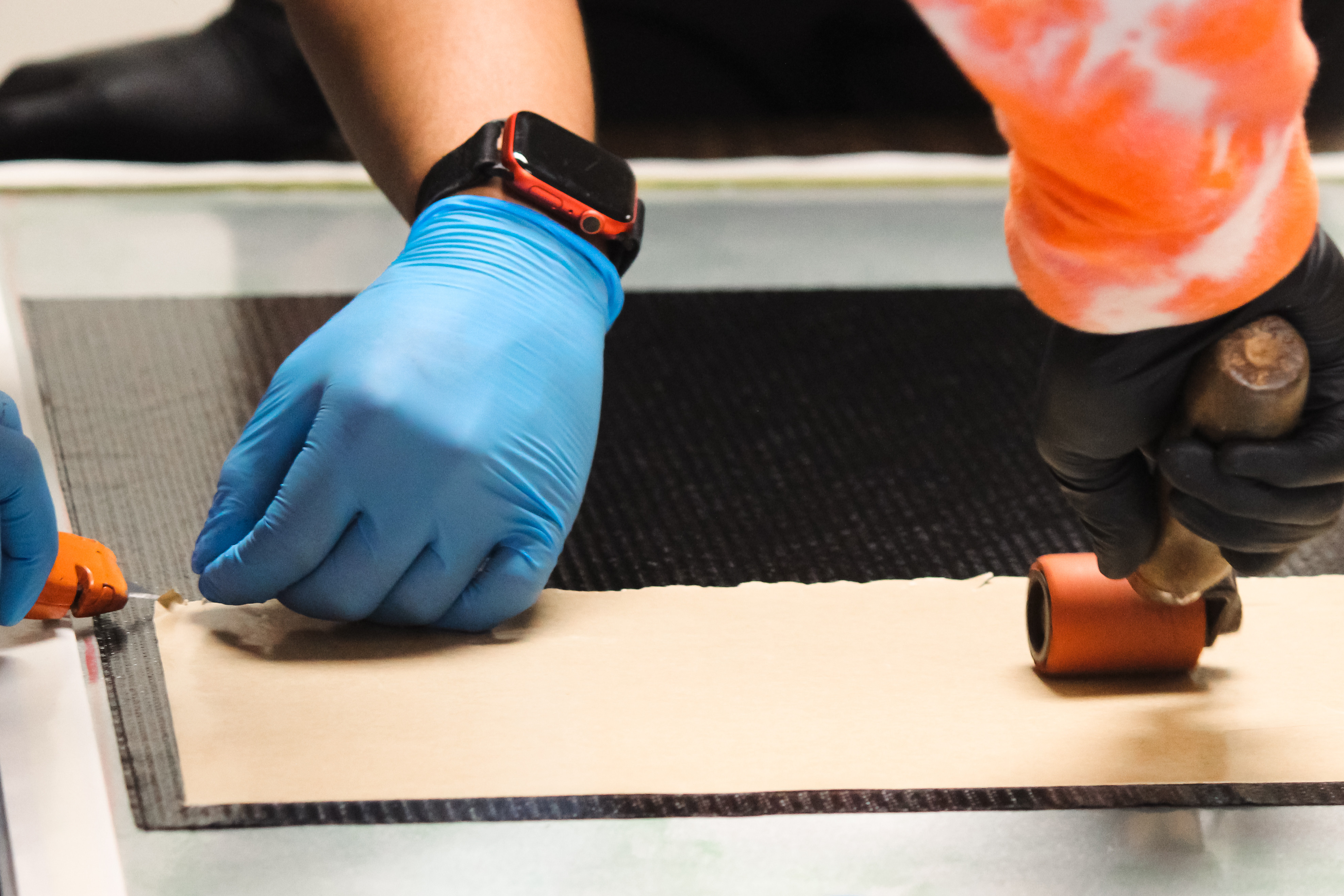
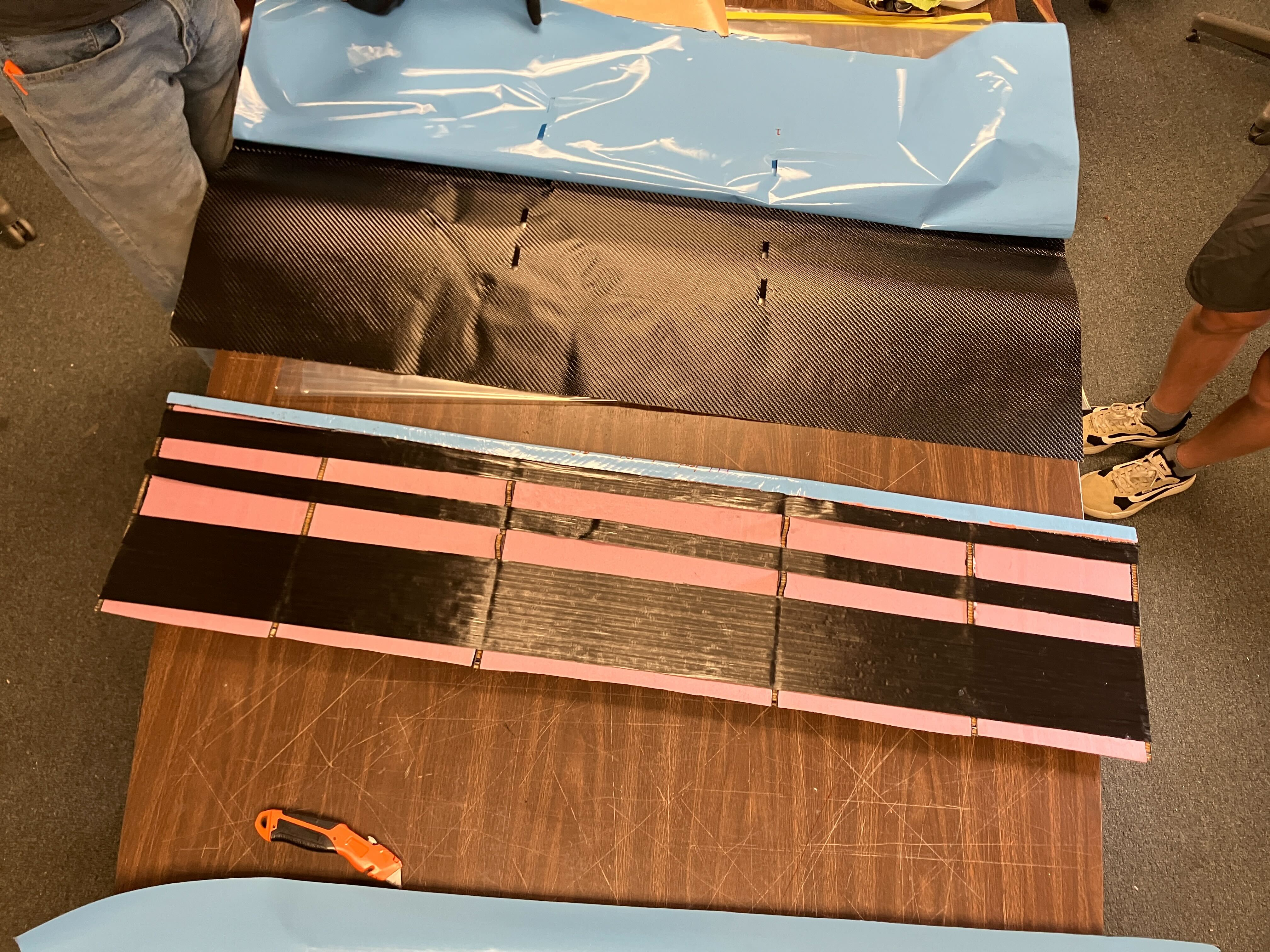
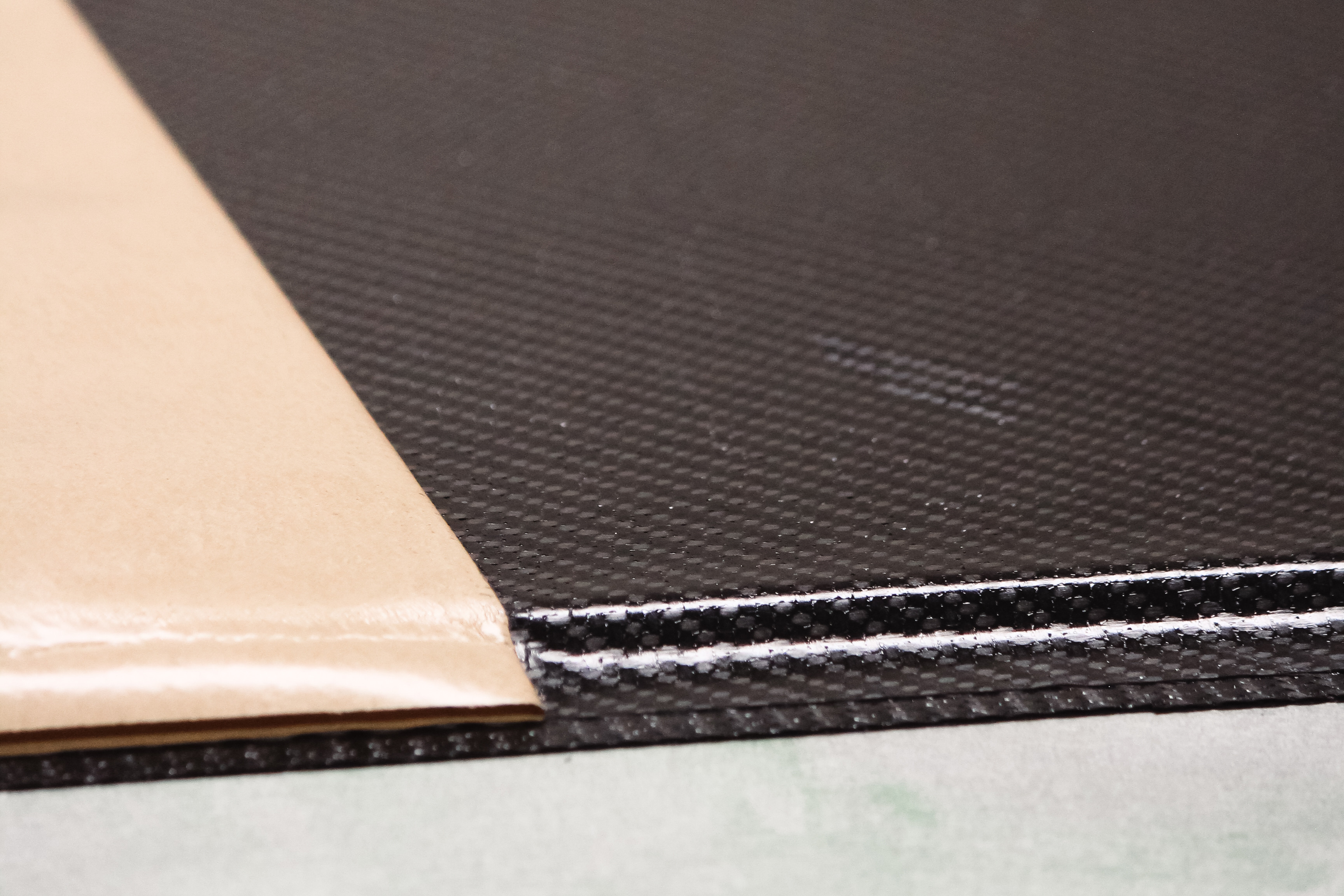